SIG presents its next generation filling technology – a technical masterpiece that’s packed with advanced innovation to optimally equip the food and beverage industry to meet today’s requirements, while at the same time offering all the capabilities to meet future challenges.
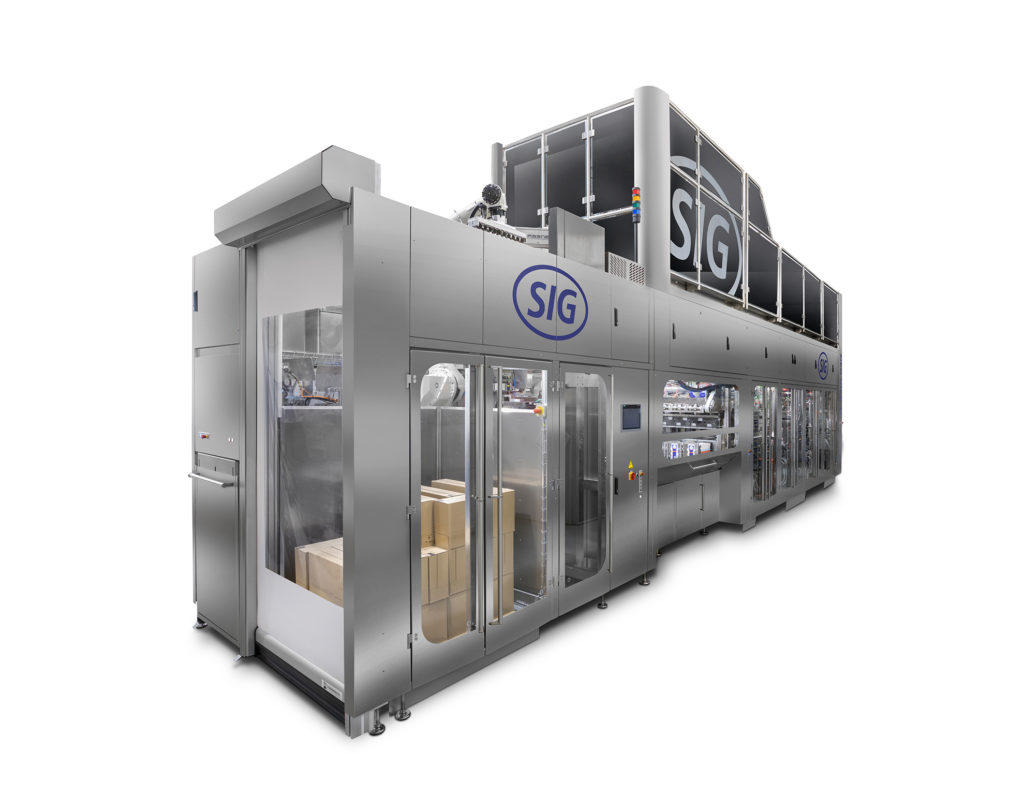
SIG NEO, making its debut with the innovative combivita family-size pack, is the centrepiece of SIG’s next generation platform and the world’s fastest filling machine for family-size carton packs with up to 18,000 packs per hour. SIG NEO has best-in-class sterility rates and reduced consumption of resources – all adding to improved total cost of ownership and a 25% lower carbon footprint compared to SIG’s current generation filling machines for family-size carton packs.
SIG’s latest filling technology innovation puts the future needs of food and beverage producers at the forefront to optimize output while helping to minimise costs.
Stefan Mergel, Senior Product Manager Equipment at SIG: “Food and beverage producers have tight deadlines, production and profitability goals, plus sustainability targets and countless KPIs to meet. To fulfil all their needs, we’ve built a world-class system that’s far more flexible and efficient than any other on the market, with industry-leading sterility rates. Driving down costs while reducing its carbon footprint, our new filling technology is better for both business and the environment – an exceptional breakthrough for aseptic filling machines.”
SIG developed SIG NEO to deliver on six core areas:
Profitability: with longer production runs, shorter cleaning times, exceptionally low waste rates and increased technical efficiency, SIG NEO is designed to deliver long-term savings and a highly competitive total cost of ownership.
Efficiency: highest speed and efficiency with an output of up to 18,000 packs per hour for family-size packs. 50% higher output compared to current generation machines but with same manpower. Unique 100+ hour run cycles, fully automated clean-in-place solution from magazine to discharge and quickest and world-class cleaning results.
Quality: best in class sterility rates with SIG’s innovative 360-degree sterilizing solution, plus an innovative transport system (SIG ZOOMER) that stays within the aseptic chamber.
Ease of use: highly intuitive user interface and a refined User eXperience [UX] (SIG CRUISER).
Flexibility: SIG has taken flexibility a step further and SIG customers can now set up the filling speed to suit production plans: either 12,000, 16,000 or 18,000 packs per hour. Automatic volume change in less than 10 minutes to run 500ml, 750ml or 1,000ml pack sizes. Ultimate product flexibility with the capability for product changes during production runs.
Carbon footprint reduction: lower carbon footprint thanks to improved waste rates and reduced use of utilities H2O2, compressed air and water (30% lower overall utility consumption), 60% water reduction and 25% reduction in greenhouse gases from filling and packaging process per filled pack.
SIG NEO provides operator independence via automatic cleaning and a built-in smart asset management system. It is intuitive to operate and will link seamlessly into any factory set up.
Perfectly complementing SIG NEO is SIG PACER, a new fully automated sleeve magazine powered by a robotic arm that works alongside customer teams to do the heavy lifting. SIG PACER takes care of detecting, gripping and opening corrugated boxes containing customer’s carton sleeves. Feeding the sleeves into the filling machine, SIG PACER maintains one full hour of autonomous production, with a complete pallet feed. This innovation sets the pace for SIG’s next generation filling line.
Finally, SIG CRUISER completes the trio of the next generation filling technology from SIG – this new user interface (Human Machine Interface – HMI) makes the entire new filling line easy to operate. The highly intuitive SIG CRUISER enables SIG customers to easily set their complete production process and is designed to make life much easier for the operator, while reducing the need for training and experience. SIG CRUISER’s user interface operates the entire filing line end-to-end, to show KPIs in an intuitive way.
Additional information:
How does SIG NEO work?
- The carton sleeves, which are pre-printed with the customer’s design and already sealed along the longitudinal seam, are fed into the six-track filling machine.
- The sleeves are pre-formed into a package shape and the closures are applied via a new integrated ultrasonic closure applicator, eliminating any need for glue to reduce cost and lower carbon footprint.
- Top and bottom of the packs are pre-folded at the predefined creasing lines.
- An innovative 360-degree solution sterilises the inside and outside, including the closure, of the entire pack to deliver best-in-class sterility rates.
- Bottom of the pack is sealed using an ultrasonic technology.
- Sterilised packs are transported into an over-pressured aseptic chamber where the beverages, which have already been sterilised in UHT units, are filled into the carton packs. New servo-driven filling station guarantees highest filling accuracy.
- The innovative transport system, SIG ZOOMER, stays within the aseptic chamber to add to first-class sterility rates.
- Top of the carton pack is sealed using the same ultrasonic sealing technology as the base of the carton, making it easier for customers to adjust and control the process.
- The upper side flaps are pre-heated by hot air and sealed to the pack. The carton pack is now tightly closed and the product is safely protected.
- Filled carton packs are then fed out from the filling machine.
Source: SIG
You must be logged in to post a comment Login