Metsä Board collaborated with industry leaders to re-design a favorite of the frozen food aisle: ice cream cone packaging. The team looked into different stages of the value chain, ranging from material production, to ink usage and logistics. The result is a packaging with a significantly lower climate impact.
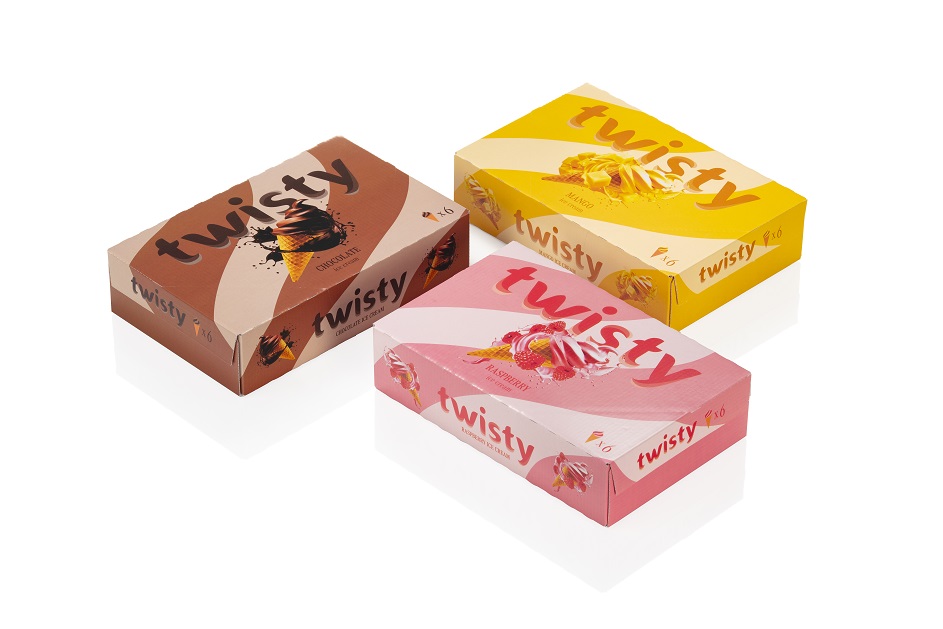
The team of design, printing and converting experts first analyzed frozen food packaging to identity areas of improvement. These solutions traditionally rely on recycled fibers and spot color printing. With this project, the team wanted to showcase new possibilities using carefully selected lightweight fresh fiber materials and flexographic printing methods to achieve excellent usability and unparalleled halftone graphics with less impact on the climate.
Metsä Board’s double coated white-top kraftliner (MetsäBoard Prime WKL, 125 g/m2) was selected as the top liner for its lightweight and smooth surface that enables excellent reproduction of detailed visuals. The inside liner and fluting were made from uncoated kraftliner (MetsäBoard Natural WKL Bright 90 g/m2) which is ideal for small and lightweight packaging requiring high strength. Both materials are made from pure and traceable fresh wood fiber making the packaging easily recyclable or compostable and safe for food packaging. Having two layers from same material also simplified production without compromising quality.
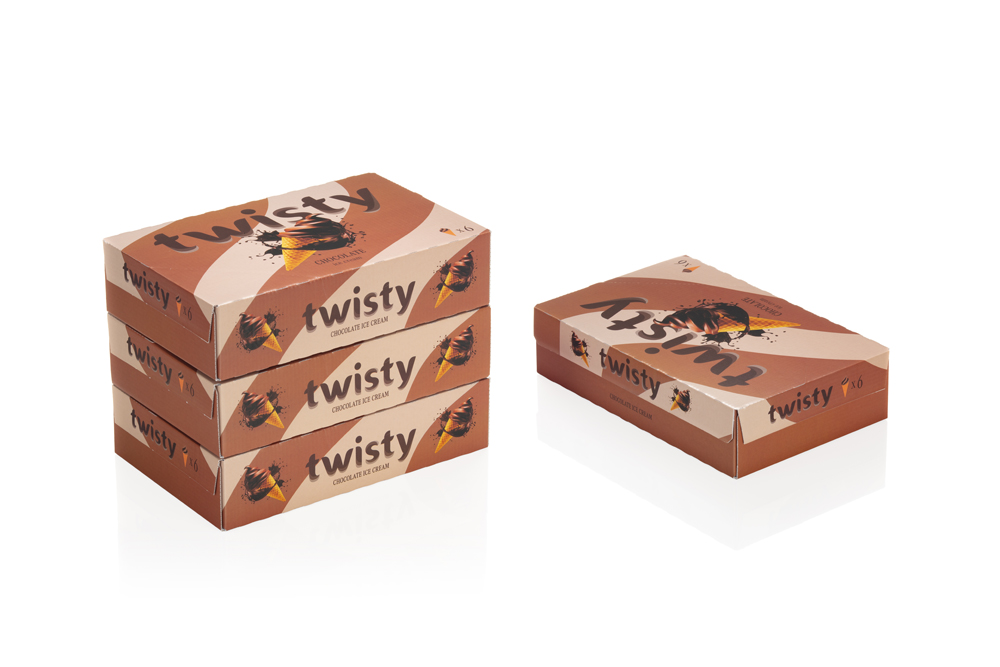
Metsä Board’s Sustainability Services did detailed calculations of the paperboard materials comparing them to traditional white lined chipboards used in the European market. Due to the 8 percent lighter weight and use of fossil free energy that is generated as a by-product of Metsä’s chemical pulp production the new packaging was found to have up to 36 percent lower climate impact (Cradle-to-Gate + End-of-Life).*
Packaging designers at Futupack paid special attention to the user experience by creating an easy-to-open design, eliminating the need for plastic parts or special tools for opening. Attention was also paid to minimizing ink usage, while keeping each variety recognizable. Process printing was selected as the printing method to eliminate the use of spot colors and enhance efficiency and flexibility.
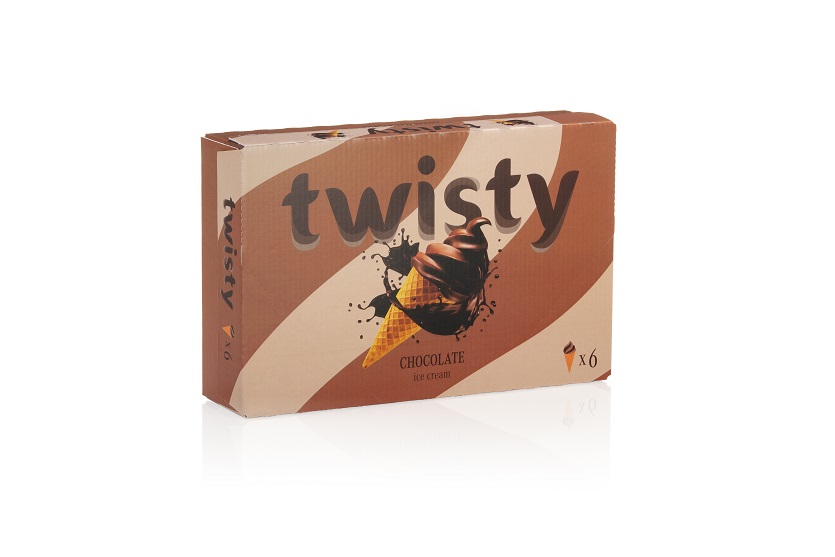
Future-ready printing methods
Packaging manufacturer Adara Pakkaus, proposed 64 lpcm expanded color gamut (ECG) co-printing as a suitable method for the corrugated board. The flexo printing plates were supplied by Marvaco. By using the carefully selected kraftliner materials, the team was able to eliminate the ‘wash board effect’ common in corrugated boards.
”This high-resolution quality is unusual in such solutions; corrugated post print typically achieves lower accuracy. ECG benefits co-printing, consolidating designs, reducing waste, plates, energy, and press return inks,” says ECG printing specialist, Dr Kai Lankinen, who consulted on the project.
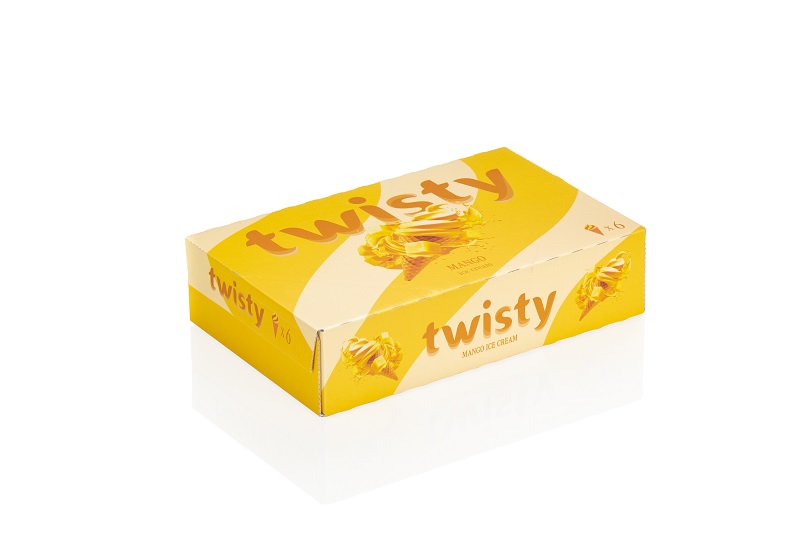
Adara’s Head of Printing Lari Seppälä noted the eco-efficiency of the project which included reviewing the entire process for selecting options to lower the environmental impacts. “With our new 7-color press and ECG tools we were able to reduce ink usage, simplify logistics and make the entire process flexible as well as cost-efficient.”
Earlier this year, the same expert team worked on another project designing the ultralight pizza box. “This ice cream packaging project showcased again the power of seamless teamwork. With the careful selection of materials, and pushing traditional boundaries of printing, we were able to combine excellent functionality and resource efficiency. Collaboration was crucial for understanding the requirements and capabilities in the different stages of the supply chain,” concludes Metsä Board’s Packaging Services Director, Ilkka Harju.
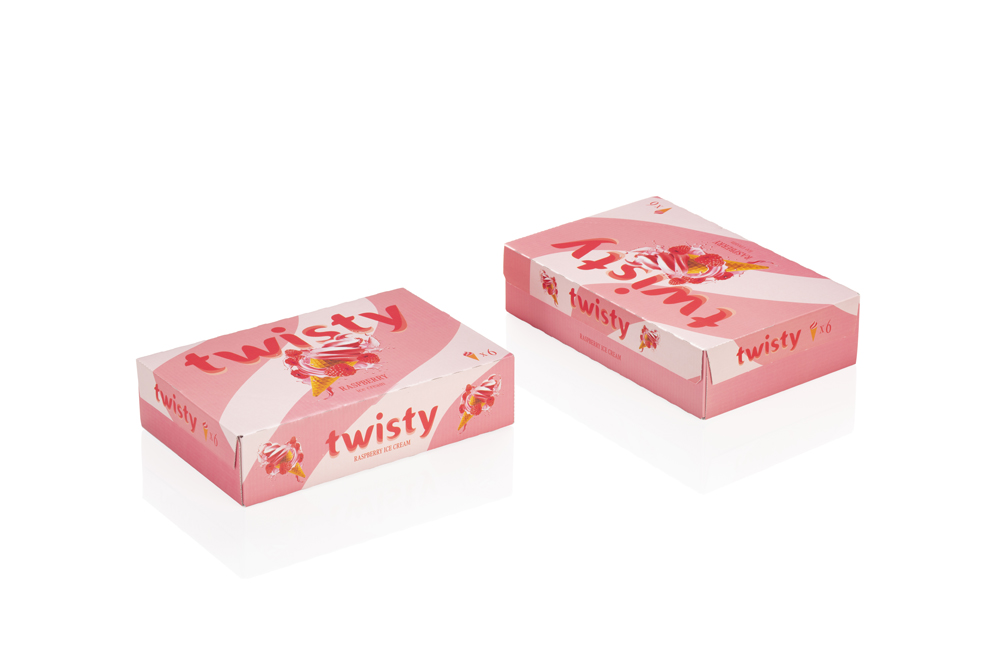
* Metsä Board follows process category rules for processed paper and paperboard which is are based on ISO 14040/14044 life cycle assessment standards when assessing environmental impacts of its paperboards. For comparative assertion external dataset from ecoinvent has been utilized. This dataset represents a typical recycled fibre linerboard on the EU markets. Comparison excludes paperboard delivery as well as printing and converting processes. End-of-life scenario is based on Finnish waste management statistics and assumed to be the same for both packaging solutions. Climate Change methodology used in the assessment was EF3.1 Climate Change – Total
Source: Metsä Board
You must be logged in to post a comment Login